The Role of Green Hydrogen in Industrial Decarbonization: A Game Changer for Heavy Industry
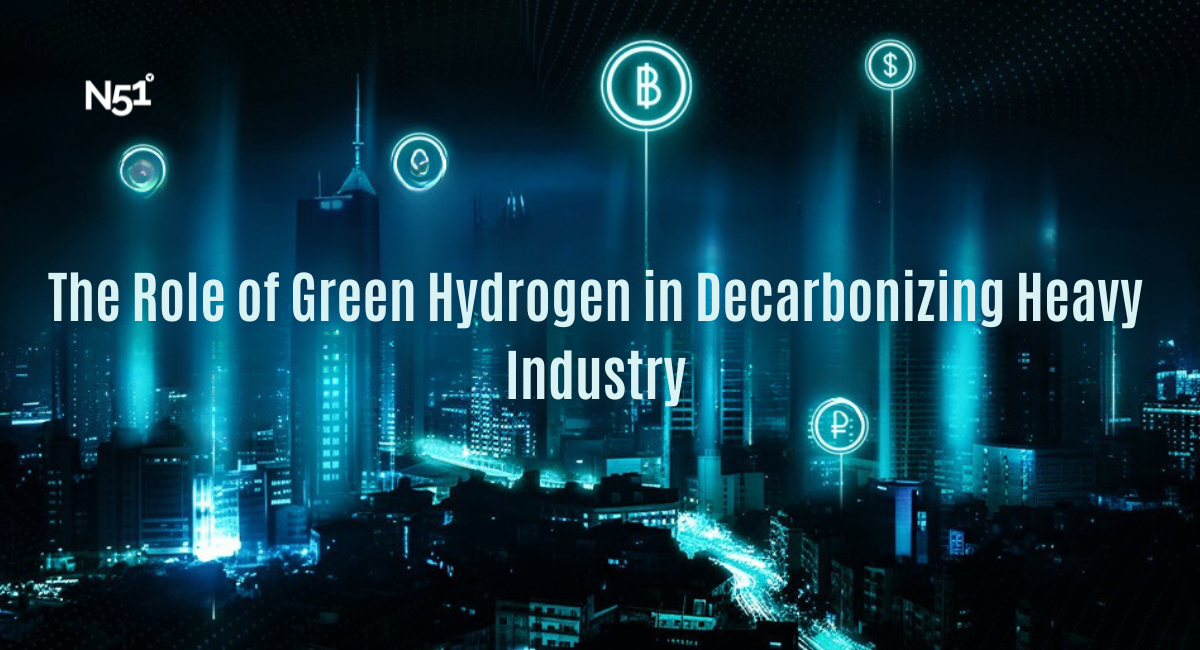
Heavy industries such as steel, cement, chemicals, and refining are responsible for a significant portion of global greenhouse gas emissions. Industrial sectors collectively contribute to roughly 20% of global CO₂ emissions, and decarbonizing these industries poses one of the greatest challenges in the transition to a net-zero economy. Green hydrogen—hydrogen produced via electrolysis using renewable energy—holds immense potential as a clean energy source to help decarbonize these hard-to-abate sectors.
In this article, we will delve into how green hydrogen can be integrated into industrial processes to significantly reduce emissions, its potential to revolutionize heavy industry, and the challenges that must be addressed for wide-scale adoption.
The Emissions Challenge in Heavy Industry
Heavy industry processes are notoriously difficult to decarbonize for several reasons:
- High energy requirements: These sectors require vast amounts of energy, often derived from fossil fuels, to operate machinery, produce heat, or drive chemical reactions.
- Process emissions: In addition to the energy consumed, some industrial processes release emissions as a byproduct of chemical reactions. For example, the production of cement results in CO₂ emissions from the calcination of limestone.
- Lack of alternatives: Many processes, such as high-temperature heating for steel and cement production, lack viable clean energy alternatives. Electrification, for example, may not be suitable for such applications due to the required energy density.
The decarbonization of heavy industry will therefore require innovative solutions, and green hydrogen is emerging as one of the most promising options.
Green Hydrogen as a Key Solution for Industrial Decarbonization
Green hydrogen can be used in a variety of industrial applications to replace fossil fuels, and its role extends far beyond merely being an energy carrier. Here’s how hydrogen can revolutionize different industrial sectors:
1. Green Hydrogen in Steel Production
Steel production is one of the largest industrial contributors to global CO₂ emissions, accounting for about 7-9% of global emissions. The traditional method of producing steel, known as the Blast Furnace–Basic Oxygen Furnace (BF-BOF) process, relies on coal to reduce iron ore into iron, producing significant amounts of CO₂.
Hydrogen-Based Direct Reduction of Iron (DRI):
- In a hydrogen-based steelmaking process, hydrogen gas is used to reduce iron ore, replacing carbon-intensive coke in the conventional process. The reaction between hydrogen and iron ore produces water instead of carbon dioxide.
- H2GreenSteel, a Swedish company, has become a pioneer in the shift to hydrogen-based steel production. They aim to build Europe’s first green steel plant, projected to reduce emissions by up to 95% compared to traditional steelmaking processes.
- Salzgitter AG, a German steel company, is another key player experimenting with hydrogen-based DRI, aiming to produce green steel at scale by the 2030s.
The successful adoption of hydrogen in the steel industry could dramatically reduce one of the most emissions-intensive industrial processes.
2. Green Hydrogen in Cement Production
Cement manufacturing is responsible for about 7% of global CO₂ emissions, primarily due to the energy-intensive nature of the process and the CO₂ emissions that occur during the calcination of limestone.
Hydrogen in Kilns:
- Green hydrogen can replace fossil fuels in the cement industry by providing high-temperature heat to power kilns. Hydrogen combustion produces water vapor instead of CO₂, significantly reducing emissions.
- While trials of hydrogen use in cement kilns are still in their early stages, HeidelbergCement is exploring hydrogen’s potential as part of its goal to reach carbon-neutral cement production by 2050. Projects are underway in Germany and Norway to assess the feasibility of hydrogen-fueled kilns.
- Another key method is Carbon Capture and Utilization (CCU), where CO₂ emissions from cement production are captured and converted back into useful products with the help of green hydrogen.
3. Green Hydrogen in Chemical Industries
The chemical industry is responsible for around 10% of industrial emissions, largely due to its reliance on fossil fuels as both an energy source and a feedstock for producing chemicals such as ammonia, methanol, and petrochemicals.
Ammonia Production:
- Ammonia is a critical component in fertilizers, and traditional production methods involve using natural gas in the Haber-Bosch process, which releases significant CO₂ emissions.
- Green hydrogen can be used to produce ammonia in a process known as green ammonia. In this process, nitrogen is combined with hydrogen produced via renewable electrolysis, resulting in ammonia with zero CO₂ emissions.
- Companies such as Yara International and Siemens are actively developing green ammonia projects, with pilot plants already operational in Norway.
Methanol Production:
- Methanol, used in the production of plastics, textiles, and other materials, can also be produced using green hydrogen. Green hydrogen is combined with CO₂ in a catalytic process to produce methanol in a carbon-neutral way.
- Carbon Recycling International in Iceland is one of the leaders in producing green methanol, using captured CO₂ from industrial processes and hydrogen from renewable energy sources.
4. Hydrogen in Oil Refining
The refining industry uses vast quantities of hydrogen to remove sulfur from crude oil, producing low-sulfur fuels that meet stringent environmental regulations. This hydrogen is traditionally produced via steam methane reforming (SMR), a process that emits large amounts of CO₂.
- Switching to green hydrogen in oil refining processes can dramatically reduce emissions associated with fuel production.
- Companies such as Royal Dutch Shell and BP are exploring ways to integrate green hydrogen into their refining processes to lower the carbon footprint of refined products.
5. Hydrogen in Glass and Ceramics Production
Glass and ceramics manufacturing is highly energy-intensive, relying on high-temperature heat from natural gas to melt raw materials. Hydrogen offers an alternative source of high-temperature heat for these industries.
- Pilkington Glass, a leading glass manufacturer, has begun trials using hydrogen to power glass furnaces as part of the HyNet project in the U.K. If successful, this could pave the way for decarbonizing glass production using hydrogen.
Challenges to Industrial Adoption of Green Hydrogen
While the potential for green hydrogen in industrial decarbonization is substantial, several challenges need to be addressed before widespread adoption is feasible.
1. Cost of Green Hydrogen:
- The production of green hydrogen remains more expensive than traditional fossil-fuel-based hydrogen due to the cost of renewable electricity and electrolyzers. However, with increasing investments in renewable energy and advancements in electrolyzer technology, costs are expected to decline significantly over the next decade.
- Government policies such as carbon pricing and subsidies for green hydrogen projects will play a key role in leveling the playing field.
2. Infrastructure Development:
- The infrastructure for producing, storing, and transporting hydrogen is still in its early stages. Building a robust hydrogen supply chain requires significant investment in pipelines, refueling stations, and storage facilities.
- Initiatives like Hydrogen Valleys in Europe aim to create localized hydrogen ecosystems, integrating production, distribution, and end-use in industrial clusters.
3. Scaling Electrolysis Capacity:
- Electrolyzer capacity must be scaled significantly to meet the growing demand for green hydrogen. Scaling production also requires the rapid expansion of renewable energy infrastructure to power the electrolyzers.
- Companies like Nel Hydrogen and ITM Power are leading the charge in scaling electrolyzer capacity, but widespread adoption will require collaboration across industries and governments.
4. Integration into Industrial Processes:
- Retrofitting existing industrial facilities to use green hydrogen can be costly and complex. Many industries may need to redesign their processes to accommodate hydrogen, requiring significant capital investment.
The Path Forward for Green Hydrogen in Heavy Industry
Green hydrogen holds immense promise for decarbonizing hard-to-abate industries such as steel, cement, chemicals, and refining. As costs decline and infrastructure develops, green hydrogen can replace fossil fuels in industrial processes, enabling these sectors to meet their emissions reduction targets.
Governments, industries, and investors must work together to overcome the challenges of cost, infrastructure, and technology development. Investments in research, demonstration projects, and policy support will be crucial to scaling green hydrogen adoption in heavy industries.
If successful, green hydrogen can provide a sustainable solution for industrial decarbonization, helping the world move toward a net-zero future while maintaining the competitiveness of these vital sectors. By integrating green hydrogen into the global industrial landscape, we can create a cleaner, more resilient economy.
Let's talk
Get in touch with us by filling the form below and one of our team members will be in touch shortly.